- 启停控制:启动前需保安过滤器压差(≤0.05MPa)、剂投加系统(阻垢剂、还原剂)及pH值(维持5-6.5)412。程序化启停设备时,需执行30分钟低压冲洗,浓水侧盐分结晶4。
- 参数监测:实时记录进水压力、段间压差、电导率及产水量,标准化产水量下降10%或压差上升15%时需触发预9。例如,5吨/小时系统产水电导率应稳定在10μS/cm以内1。
- 剂管理:阻垢剂采用氨基三亚甲基膦酸(ATMP)或聚丙烯酸(PAA),投加浓度2-5ppm;化学清洗时选用pH1.5-2的柠檬酸或pH10-11的EDTA钠盐溶液,温度控制在38-41℃49。
三、维护与清洗策略

- 操作规范:有限空间作业需执行“先通风、后检测、再作业”流程,硫化氢浓度需<10ppm,并配置正压式呼吸器5。
- 故障处置:膜壳裂时立即关闭进水阀,启动备用水源;微生物污染采用0.1%亚硫酸氢钠浸泡12小时,配合50℃热水循环菌94。
- 应急演练:每季度开展膜组件泄漏、触电及化学品灼演练,重点培训CPR急和洗眼器使用512]。
六、应用场景扩展
在半导体行业需增加二级RO+EDI模块,产水电阻率≥18MΩ·cm;饮料行业宜配置UV菌和臭氧发生器,菌落总数控制<10CFU/ml16]。针对海水淡化系统,可引入压力式超滤作为预处理,结合SWC5系列海水膜,脱盐率可达99.8%79]。

- 物理维护:每日冲洗膜表面15分钟,每周密封圈及O型圈,每月更换5μm保安滤芯312。机械过滤器需定期反洗,反洗度8-10L/(s·m²),时长15-20分钟5。
- 化学清洗:分酸洗(去除碳酸钙/金属氧化物)和碱洗(清除有机物/生物膜)两阶段。典型程序包括:循环清洗1小时、浸泡4-6小时、再循环30分钟,清洗流量按膜厂商额定值的50%设定94。重度污染时可使用0.1%非离子表面活性剂化清洗效果9。
- 膜更换标准:当标准化产水量低于设计值30%、脱盐率下降至95%以下或化学清洗频率超过2次/月时需更换膜元件3。
四、能耗与成本优化
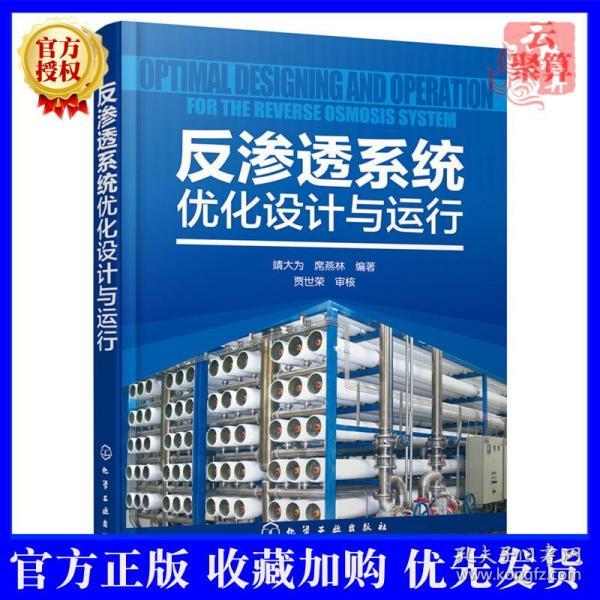
- 能量回收:针对浓水压力≥0.7MPa的系统,推荐安装PX型能量回收装置,可降低高压泵能耗35%-40%1。
- 水回用率控制:通过调节浓水排放阀,将系统回收率稳定在75%-80%,高硬度水源(Ca²⁺>200ppm)需降至60%以下89。
- 智能控制:集成PLC与SCADA系统,实现阻垢剂投加量、冲洗频率与水质参数的联动调节,典型例显示可降低剂成本18%512]。
五、安全管理与应急预

一、系统设计与工艺流程
反渗透系统的心工艺包括预处理、高压泵增压、膜分离、浓缩液处理及产水储存等环节1。预处理阶段需根据原水水质配置多介质过滤器、活性炭吸附或软化装置,确保进水SDI≤5、余氯≤0.1ppm,以保护反渗透膜912。高压泵需选用耐蚀材质,配置电动慢开阀防止水锤冲击,并通过变频器调节压力至1.0-1.5MPa,平衡产水率与膜寿812。膜组件推荐采用抗污染复合膜,6芯装8040规格膜壳,设计通量控制在15-22L/(m²·h),串联式排列可提升脱盐率至99%以上17。

二、日常运行管理
反渗透运营方
相关问答
文章来源:
用户投稿
版权声明:除非特别标注,否则均为本站原创文章,转载时请以链接形式注明文章出处。